Proven cutting-edge technology utilizing a specialized hydrocarbon-extraction/de-greasing agent and final oil-containment coating for use on oil-contaminated concrete surfaces.
This specifically engineered oil-removal and containment process rehabilitates industrial surfaces rendering them suitable to receive any type of flooring system.
Due to various activities, industrial floors can be oil/fat contaminated to a depth of several inches. A system has been developed to deep-clean and coat these floors started by mechanically removing surface contamination on layers, thereby exposing surface voids for subsequent deep cleaning.
The prepared surface will be deep-cleaned with our specially developed VAP 1® ORS-D detergent that is power-washed into the concrete to ensure adequate removal of oil to a substantial depth. Finally the specifically formulated VAP 1® ORS-C Oil-Resistant coating will be applied to block any further migration of the oil to the surface.
After a minimum cure period of 16 hours, final coatings such as polyurethanes, epoxies, resilient flooring to underlayments, etc. can be applied onto our VAP 1® ORS-C Oil-Resistant coating.
The cleaning and coating applications can take place in sections. This allows for application without causing disruption to building activities or problems without production/traffic. All products are VOC compliant.
Advantages to this Procedure
- As the test cores indicate, cleaning can take place to considerable depth without damage to concrete.
- Concrete will not lose alkalinity.
- During application there are no toxic fumes, dust or disruptive noise.
- No excessive cleanup is necessary.
- Easy disposal according to the local and federal regulations.
- No interruption of other activities.
AN OIL-REMOVAL AND CONTAINMENT PROCESS TO REHABILITATE CONCRETE SURFACES RENDING THEM SUITABLE TO RECEIVE ANY TYPE OF FLOORING SYSTEM
Description
- One-coat of special oil resistant coating (ORS-C) and special detergent (ORS-D).
- Combined, they provide a dry, uncontaminated surface fit to receive flooring/coating systems.
- Has ability to penetrate deep into concrete surface, extracting oil leaving a clean surface for the ORS-C Coating.
- Detergent is forced into concrete with a “spinner.”
Preparation of Substrate
- Substrates receiving KOESTER VAP I® ORS SYSTEM must meet acceptable industry standards as defined in ACI Committee 201 report “Guide to Durable Concrete.”
- Oily wastewater must be vacuumed into containment tanks and repeated until all oil is removed from the concrete slab.
- Oily wastewater must be disposed in accordance with local and state regulations.

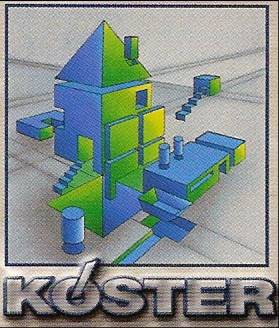
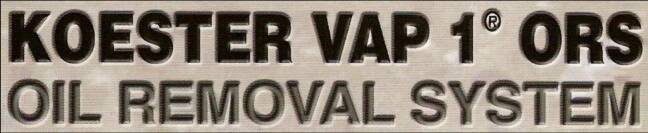
LIMITED WARRANTY: KOESTER AMERICAN CORPORATION (“KOESTER”) warrants that its products shall be in accordance with their published specifications and covenants that, in the event any of its products fail to meet their published specifications or their published performance standards (subject to published conditions such as proper application and surface preparation), KOESTER shall replace those products proved defective, but Koester shall not be responsible for consequential damages due to the breach of its warranties notwithstanding the foregoing, KOESTER’S liability hereunder shall not exceed one and one-half (1½) times the cost of the defective product originally purchased.
EXCEPT AS SET FORTH ABOVE, KOESTER MAKES NO OTHER WARRANTIES, EXPRESS OR IMPLIED, AND MAKES NO WARRANTY AS TO MERCHANTABILITY OR FITNESS FOR A PARTICULAR PURPOSE.



Relative Humidity Test “In Situ"
Wine Country Shotblast and Coatings provides all in house testing prior to any and all flooring product installations. We, at Wine Country Shotblast and Coatings follow all ASTM F2170-02 Standard for Determining Relative Humidity in Concrete Floor Slabs Using In Situ Probes.
The process involves drilling approximately 2-inch-deep holes in the concrete to measure the humidity inside.
Scientific testing has shown that the Calcium Chloride test only measures the vapor emissions from the top 1 inch or so of the concrete slab. Others claim only the first ¼” from the top. Because most concrete dries from the top down, the calcium chloride test may miss moisture deep inside the concrete that is likely to rise to the surface after a floor covering is installed. For this reason, many now consider the RH test a better predictor of future moisture problems.
With the installation of the In Situ probes, Wine Country Shotblast and Coatings can return frequently to check the status of the slab, after the first installation and acclamation of the first 72 hours. Manufacture probes contain its own battery which will allow up to hundreds of reading. Construction superintendents now have the availability to frequently view the probes and make sound recommendations in order to stay on time and on track with no costly surprises after the installation.
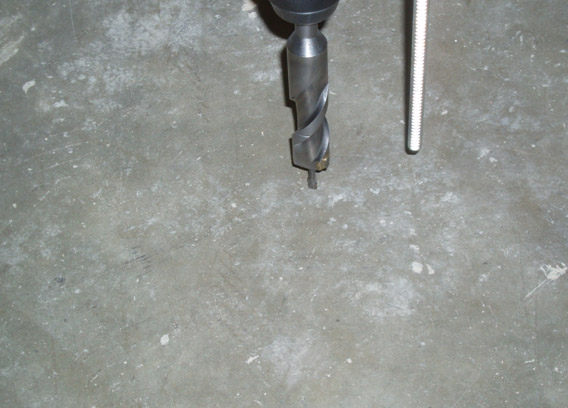
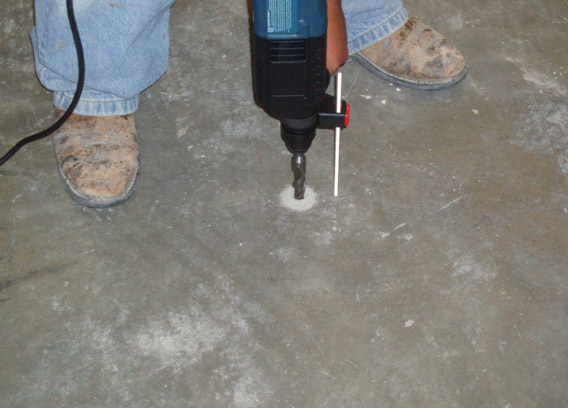
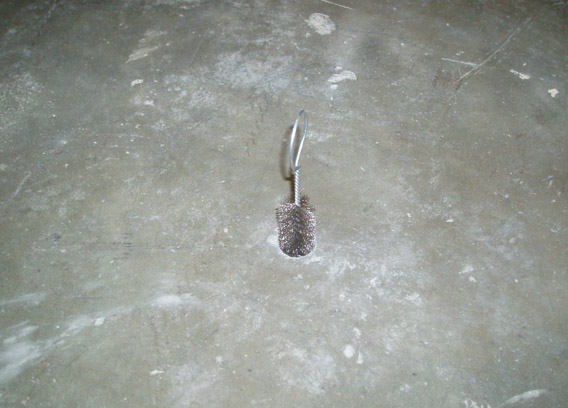
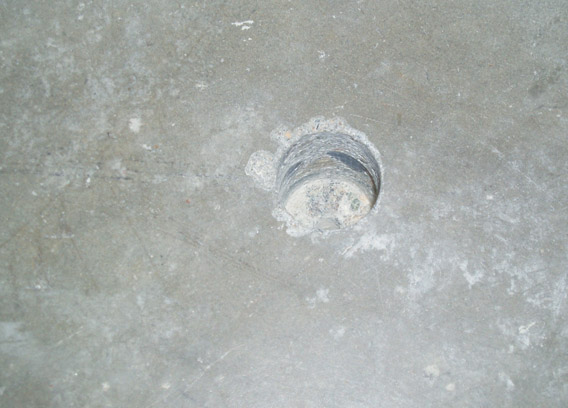
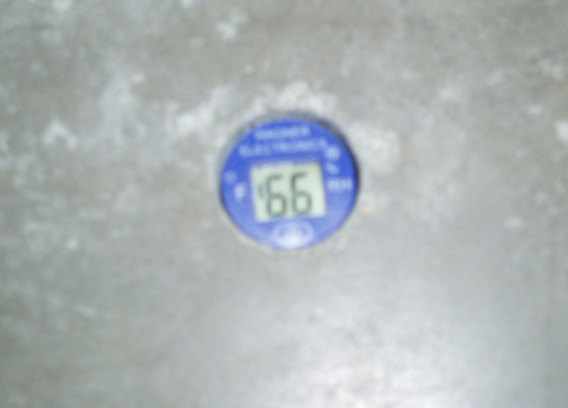
Calcium Chloride Testing
Wine Country Shotblast and Coatings. provides calcium Chloride testing prior to any and all floor systems installed. This is a widely used and recognized test. Basically, it has served as a standard in the flooring industries for several time. Most installation companies are yet to familiarize them self with Relative Humidity testing. The calcium chloride (CC) testing was the best test of its time.
The calcium chloride vapor emission test was developed over 40 years ago to quantify the volume of water vapor radiating from a concrete slab surface over time. This has been used to measure the amount of moisture that emits from a given 1,000 SQ. FT. of slab surface over a 24 hour period. The result is expressed as “pounds” which is the equivalent weight of water, emitted as vapor, over 1,000 SQ. FT. within 24 hours. This test requires the use of a gram-weight scale with a gradation of 1/10th (0.1) gram. The calcium chloride container is weighed before and after exposure to the concrete slab. It is highly recommended that the test be
weighed prior to, and directly after exposure on the same scale. This is a very sensitive test when conducted in an ideal environment.
Differences between the two scales and extended time between weighing can offset the test result. While the test can measure moisture in a wide range of building climates, the results are only meaningful when conducted in a similar building environment
as the finished floor system. Obtaining meaningful results is only possible when tests are conducted in a representative interior climate.
Crack and Joint Repair
Wine Country Shotblast and Coatings incorporates the repair of existing cracks and construction joints prior to the installation of Koesters VAPI-2000 and the pH Water Vapor and Alkalinity Control Systems.
We, at Wine Country Shotblast and Coatings, also have the capabilities of pumping self leveling SLV- urethanes and polyurea joint fillers.
Solving yesterday’s Water Vapor and Alkalinity problems with today’s technology
Wine Country Shotblast and Coatings is a Certified Installer of the Koester products and VAPI®-2000 Water Vapor and Alkalinity Control System, a one-coat system consisting of a unique combination of epoxy resins. It specifically formulated to overcome the poor long-term adhesion properties of most resin-based systems when in an environment of constant wetness, extreme alkalinity (12-14pH) and water vapor drive. Because of its extreme density, we are capable of reducing water vapor and moisture to levels acceptable of most coatings, adhesives and floor covering systems by 94%.
Coupled with our full service floor preparation, it’s a combination win-win situation. With 30 years of true hands on experience and equipment capabilities, our services provide for a solid substrate and longevity for your flooring system.

Wine Country Shotblast and Coatings
(707) 253-9262 phone & fax
1010 Stonedge Drive, Napa, CA 94558
www.winecountryshotblast.com
Copyright © 2009 Wine Country Shotblast and Coatings All rights reserved |1010 Stonedge Drive, Napa, CA 94558 | 707-253-9262
Wine Country Shotblast and Coatings
(707) 253-9262 phone & fax
1010 Stonedge Drive, Napa, CA 94558
www.winecountryshotblast.com